Glossary
In this glossary, you will find an overview of all the technical terms we use on this website to explain our research. In addition, we have added terms that are helpful in connection with the research wind farm (WiValdi) and renewable energy sources.
A – F
An acceleration sensor detects the acceleration acting on the sensor. By evaluating the acceleration, the movement of the sensor can be calculated. A combination of several sensors can thus detect the exact position and movement of a body in space.
Aerodynamics is the study of the ‘force of air’ (Greek aero = air, dynamis = dynamics), and describes the behaviour of objects (such as rotor blades) in air. In addition to flying bodies, the use of wind energy – for example for sailing or power generation – also belongs to the field of aerodynamics.
The scientific field of aeroelastics encompasses the physical processes occurring in structures around which air flows when the aerodynamic loads interact with the elastomechanical forces in the structure. Aeroelasticity in wind turbines describes the deflection of the rotor blades under wind load in particular, but also previously little-described phenomena such as flutter.
An anemometer is a measuring device for determining wind speed. Different types of design are used. Classic cup anemometers and ultrasonic anemometers are the most common.
The angle of attack of a wind turbine describes the angle at which the rotor blades are positioned relative to the wind. The angle of attack is influenced by the pitch angle, rotor blade speed, and wind velocity. It is adjusted to regulate the performance and efficiency of the turbine. A shallow angle of attack is used at low wind speeds to generate sufficient lift. At higher wind speeds, the angle of attack is increased to turn the blades away from the wind. This reduces the lift force that can be converted into rotational motion of the rotor blades, causing the wind turbine to either decrease in power or maintain a constant power output as the wind speed increases.
When a gust of wind hits a rotor blade, the rotor blade bends and is thus heavily loaded. If, due to a specific structure in the rotor blade, the rotor blade also twists axially (under torsion) during deflection, this is referred to as bending-torsion coupling. With axial torsion, the blade is turned out of the wind and thus the aerodynamic loads are reduced. This principle has the advantage that the load peaks acting on the wind turbine during a gust of wind are reduced and the wind turbine can therefore be designed to be less ‘robust’. This saves on materials and costs.
This refers to the continuous monitoring of a machine (wind turbine in this case). Mechanical components in particular, such as bearings, are extensively equipped with sensors to be able to provide information about their condition at any time. Through constant monitoring, maintenance work can be better planned and downtime minimised, as components can be replaced before they fail.
With an efficiency improvement, an attempt is made to gain more benefit from the energy used (see energy efficiency). For the same energy input (in this case – the same wind strength), an attempt is made to produce more electrical energy. This can be achieved through aerodynamics (for example, better rotor blade designs), mechanical improvements (for example, less friction in the gearbox), better control (for example, intelligent use of wind gusts or turbulence), operational changes (for example, less downtime due to maintenance) and other measures. For wind turbines, improving efficiency means that more electricity can be generated without having to increase the size of the wind turbines. In order to meet the growing demand for energy, facilities must become increasingly efficient, because this is the only way to implement a sustainable energy supply system in the long term.
Emission (from the Latin emittere = to send out) is another word for discharge. This usually refers to emissions of particles, substances, noise or radiation (for example, light) into the environment. Pollutant emissions caused by humans are called anthropogenic emissions. Sound is emitted during the operation of wind turbines, mainly due to air turbulence on the rotor blades.
The term efficiency refers to the relationship between benefit and effort. Energy efficiency measures the benefit in relation to the energy used. In a wind turbine, the energy used is the energy of the wind (kinetic energy of moving air), and the benefit is the electricity produced (electrical power). Since losses always occur during the conversion of energies, the electrical power is less than the kinetic energy applied. Therefore, the more electrical energy produced with the same amount of wind means increased efficiency.
These are sensors in which the measured variable is transmitted optically. A light source (usually a laser or LED) is connected to an optical fibre and a detector. The optical properties of the fibre are changed by the desired measured variable (for example, polarisation, fluorescence, absorption). If the optical fibre is now influenced by the measured variable, the light is influenced in polarisation, phase or intensity. With this principle, fibre-optic sensors can record a wide variety of measured variables, such as strain, vibration and temperature.
Full load refers to the operation of a power generation plant at maximum output. For electricity generation, these are usually turbines. If they are operated at less than full power, this is referred to as partial load.
G – N
Greenhouse gases are gases in the atmosphere that affect Earth’s energy balance. The Kyoto Protocol applies to six greenhouse gases: carbon dioxide (CO2), methane (CH4), and nitrous oxide (N2O), as well as the fluorinated greenhouse gases (F-gases): hydrofluorocarbons (HFCs), perfluorocarbons (PFCs), and sulphur hexafluoride (SF6). Nitrogen trifluoride (NF3) has also been included since 2015.
In Germany, carbon dioxide accounts for 88.0 percent of greenhouse gas emissions, methane for 6.1 percent, nitrous oxide for 4.1 percent and the F-gases for around 1.7 percent (figures from 2018). The increasing concentration of greenhouse gases in the atmosphere prevents the reflection of solar radiation on Earth’s surface, thus causing the temperature in the atmosphere to rise.
Hub height refers to the height of the hub (centre of the rotor) above the surface of the ground. Broadly speaking, hub height describes the size of a wind turbine without the rotor blades. Since the wind speed, and thus the energy yield, increases with height, wind turbines are being constructed to be progressively higher – as far as this makes sense from a technical and economic perspective.
IEC 61400 is the most important standard for wind turbines published by the International Electrotechnical Commission. This standard contains technical requirements for designs and is intended to ensure that equipment is properly developed and operated without causing damage to people and machinery. IEC 61400 also includes, among other things, requirements on how to determine wind conditions on site and is thus also applicable to wind measurement on meteorological measurement masts.
Light Detection And Ranging is a laser-based optical method for measuring wind speed, wind direction and turbulence. The emitted laser beam is reflected by particles in the air, the frequency shift of the emitted and received laser beam provides information about the movement of the air at this point (Doppler effect). The laser beam is directed very rapidly to different points so that exact information can be provided at any time about the wind speed and direction in front of a wind turbine.
Meteorological measurement masts are used to record weather events on the basis of physical and chemical data collection. The most important variables recorded on the masts, which are up to 150 metres in height at the research wind farm in Krummendeich, are wind speed, wind direction, temperature, air pressure, humidity and precipitation.
Micrometeorology studies short-lived and small-scale phenomena of meteorology, such a turbulence and wind fields. An important aspect is also the movements in the boundary layer, such as heat exchange between the ground and the different air layers, as well as the mixing of the air layers by near-ground turbulence. In addition to anemometers and temperature sensors, one of the most important instruments for detecting turbulence is LIDAR.
O – T
Piezoelectricity is a physical effect in which electrical charge is generated when a certain material is subjected to force (piezo ignition). Piezoelectric sensors can use this effect to detect very small deformations, such as vibrations. However, this effect can also be reversed, that is, a piezoelectric sensor that is electrically excited acts as an actuator and emits vibrations (Lamb waves).
Many of these sensors are evenly distributed over a larger area in the rotor blades in piezoelectric sensor networks. One of the sensors (the actuator) emits Lamb waves and all other sensors receive these vibrations. If there are defects in the structure (for example, a crack), the vibrations are not transmitted unchanged. This interference is detected when the vibration received by the individual sensors is evaluated. This makes piezoelectric sensor networks a tool for structural health monitorings and helps to immediately detect and localise defects in the rotor blade.
The power curve describes the characteristic behavior of a wind turbine and the electrical power generated at the respective wind speed. Below the cut-in wind speed (usually in the range of 3 m/s or 11 km/h), the turbine is at a standstill. However, the rotor blades are not locked and idling. When the cut-in wind speed is reached, the rotor blades start to turn - the turbine operates is in the partial load range.
The stronger the wind blows; the more electricity is produced. When the rated wind speed is reached (usually in the range of 10 - 15 m/s or 40 - 50 km/h), the turbine generates its maximum power - it is in the full load range. If the wind now becomes stronger, the rotor blades are pitched out of the wind by the pitch system and the power remains constant. When the cut-out wind speed is reached during heavy storms (usually at 25 m/s or 90 km/h), the rotor blades are pitched completely out of the wind and the turbine stands still to prevent damage.
Power-to-X technology (also referred to as P2X) converts electrical energy from renewable energy sources such as wind turbines (power) into another form of energy (X) that can be better stored and transported. Usually, electrolysis is used to convert electrical energy into a fuel gas such as hydrogen or methane (power-to-gas). Since gas can be stored much more cost effectively than electricity, in times of overproduction (sun shining, strong wind blowing, little consumption) the surplus electricity can be converted into gas and stored.
In times of electricity deficit (no sun, no wind), the gas can either be burned in gas-fired power plants to generate electricity again, or used for the heat (gas heating) or transport (hydrogen vehicle) sectors. The main challenge with Power-to-X technology relates to efficiency. Both electrolysis and combustion are physically only feasible with considerable losses. Its use is therefore currently economically difficult and only makes sense in the event of a high energy surplus.
Predictive Maintenance optimizes maintenance schedules based on information from sensor measurements of the condition monitoring system. This information can be used to predict the time until the occurrence of an error and thus the remaining time until the next necessary maintenance. Predictive maintenance prevents unnecessarily short maintenance intervals while also guaranteeing safe, error-free operations.
Prescriptive Maintenance changes a control algorithm to react to information from sensor measurements of the condition monitoring system. These adaptive control interventions guarantee safe, efficient operation even with minor damage until the next scheduled maintenance and prevent failures. In contrast to predictive maintenance, the maintenance schedule remains unchanged. This is important when the maintenance work cannot always be carried out - such as in an offshore wind farm in winter.
Renewables are energy sources that are inexhaustibly available or rapidly renewable on a human timescale. These include wind energy, solar energy, bioenergy, hydropower, geothermal energy and environmental heat.
The Research Alliance Wind Energy, founded in 2013, combines the know-how of more than 600 scientists and generates groundbreaking stimulus for the energy supply of the future. The three partners – German Aerospace Center (DLR), ForWind – the Center for Wind Energy Research of the Universities of Oldenburg, Hanover and Bremen and Fraunhofer Institute for Wind Energy Systems (Fraunhofer IWES) – are able to successfully carry out major long-term and strategically important projects, thanks to their manpower and strong ties to major industry players, politics and research institutions.
This wide basis of expertise supports the German wind energy industry in asserting its leadership in engineering and its competitiveness on an international level. The community of the research alliance has an international charisma and opens up synergies for upcoming major projects in the wind industry, which is increasingly making its processes more commercially oriented.
To replace fossil fuels, electricity from renewables must be used in all three sectors (electricity, heat, transport). Sector coupling is a promising solution for a comprehensive decarbonisation of energy consumption. The electricity generated from renewables could thus also be used for transport (for example, electric cars) and for heating (for example heat pumps).
Wind turbine rotor blades have become increasingly large within the last few years. However, the advantage of higher energy production means that they are exposed to highly fluctuating and varying loads. Smart rotor blades are intended to make the turbines lighter and more durable despite their size.
Smart rotor blades can adapt their geometry to the local wind effects in terms of load reduction and yield increase. They work using active or passive technologies. With the passive approach, for example, a rotor blade twists in strong winds and thus provides the wind with a reduced contact area. As one of the active solutions, movable vanes on the rotor blade can improve the efficiency of wind turbines under highly fluctuating turbulent wind conditions. The trailing edges of a rotor blade can also change and thus react directly to gusts and compensate for vibrations.
The term sound exposure is used to describe the effect of noise on the environment or on humans.
Strain gauges are sensors affixed directly to the material to be tested to detect the strain and compression of the object. The strain gauge consists of a resistance wire that is elongated when the object is stretched. Due to the elongation, the resistance wire changes its electrical resistance. This measurable change allows the deflection to be calculated precisely.
Structural health monitoring is a method of monitoring certain components of the wind turbine (predominantly the rotor blades) for their ‘structural health’, so that cracks or other damage in the structure are immediately detected and localised. A piezoelectric sensor is one of the tools used for this.
Turbulence is the term used to describe the displacement of flow caused by obstacles. Turbulence occurs when uniform (laminar) flow meets terrain structures or rotor blades, for example. The rotor blades create a turbulent flow behind a wind turbine, which only returns to a steady flow again at a certain distance.
U – Z
A wind turbine takes the energy of the wind and converts it into electricity. The air flow behind a wind turbine (the wake) is thus lower, that is the wind speed decreases. An arrangement of wind turbines where on is positioned wake of another is normally avoided, as the increased turbulence and reduced wind speed there lead to a reduced energy yield. The objective is to use research and experiments to control wind turbines in such a way that as much energy as possible can be generated in the wake despite the increased turbulence.
Wind energy is the use of wind power as an environmentally and climate-friendly source of electricity generation. Alongside solar energy, wind energy is considered the most important pillar of a global energy transition, due to its widespread availability and low electricity production costs. A distinction is made between onshore wind energy and offshore wind energy.
Wind turbines require a certain cut-in wind speed (usually in the range of 3 m/s) for the rotor to rotate. From this wind speed on, the wind turbine is in the partial load range. The rated wind speed (usually in the range of 10 - 15 m/s) is the wind speed at which the wind turbine can generate its rated power (full load). If the wind speed continues to increase, the rotor blades are slowly pitched further and further out of the wind (see pitch system), so that the wind turbine continues to generate the maximum power constantly despite the increasing wind speed. From the cut-out wind speed (usually in the range of 25 m/s), the rotor blades are pitched completely out of the wind and the wind turbine stops to avoid damage.
A wind turbine converts the energy of the wind into electrical energy through aerodynamic effects. The design with a horizontal axis and three rotor blades has become widely accepted – both onshore and offshore. A wind turbine consists of the following components:
Rotor blade
The rotor blade is the most crucial component of a wind turbine. When the wind hits the profile of the rotor blade, lift is created, and the blade moves (in a similar way to an aircraft wing). Most wind turbines have three rotor blades.
Nacelle
The nacelle is located at the top of the tower and houses all the components required to operate the wind turbine.
Pitch system
A pitch system (blade angle adjustment) is used to turn the rotor blades on the hub. Changing the angle to the wind direction also changes the output of the wind turbine. When the rotor blades are turned away from the wind, the wind turbine stops. The pitch system makes it possible to start, stop and regulate the output of the wind turbine.
Main bearing
The main bearing is the bearing that supports the rotor shaft between the hub and the generator.
Azimuth bearing
The azimuth bearing supports the nacelle on the tower and uses a drive system to ensure that the nacelle and the rotor are aligned with the direction of the wind.
Generator
The most important electrical component, the generator, converts the energy of the rotor shaft into electrical current.
Inverter / transformer
The inverter and transformer convert the electricity generated in the generator so that it can be fed into the national electricity grid.
Hub
The rotor blades are mounted on the hub. The hub connects the rotor blades to the rest of the machinery and transfers the output of the rotor blades to the rotor shaft.
Tower
The tower of a wind turbine can have a variety of shapes and might be made of different materials. Most modern wind turbines have a tower made of either steel or concrete. Hybrid versions are also possible.
Foundations
This underground part of the wind turbine anchors it to the ground and provides stability. Depending on the soil quality, there are different types of construction, for example pile foundations or flat foundations.
The research wind farm in Krummendeich is funded by the Federal Ministry for Economic Affairs and Climate Action (BMWK) and the Lower Saxony Ministry of Science and Culture (MWK).
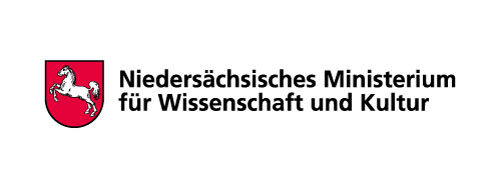
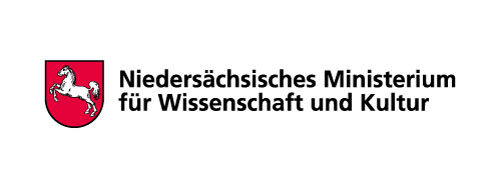